CHEMICAL INDUSTRY
The chemical industry has a high demand for the filter system and the structure of the filter press used. The entire system must be resistant to both chemical and mechanical corrosion to provide the highest possible end product quality. Therefore, the technological solutions that ensure the durability, safety and filtration performance of the machine are best designed for chemical filtration solutions.
WESTER FILTER offers comprehensive filter press technologies – precise in solid-liquid phase separation, helping customers improve production to provide the highest quality of filtration. Our filter presses and membrane filter presses are also suitable for mechanical properties at temperatures from – 10 degrees C to 95 degrees C, maximum filter pressure from 8 to 14 Bar.
We are committed to bringing you products with high stability, filtration speed coupled with great filtration efficiency. The input data parameters are tested and thoroughly controlled by us through professional screening and calculation stages. Therefore, the investment efficiency will be maximized for customers, the stability of the system is achieved at the highest level.
The important process steps of the WESTERN FILTER filter press are: Feeding, Filtering, Dewatering, Drying.
SOME TYPICAL APPLICATIONS OF THE FILTER PRESS FOR CHEMICAL INDUSTRY
In Vietnam, acid production plants are distributed in industrial parks and industrial clusters in Hai Phong, Quang Nam, Hanoi, Binh Duong, etc., serving many different needs in production and processing.
In order to increase the quality of the finished acid, the filtration stages are mainly used as fog filter towers and filter bags.
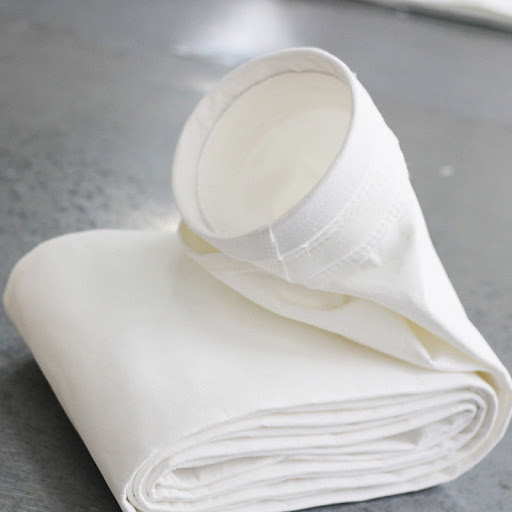
- Advantages: Low investment cost, low price.
- Disadvantages: Relative filtration efficiency, only suitable for small scale and only used with low acid concentration.
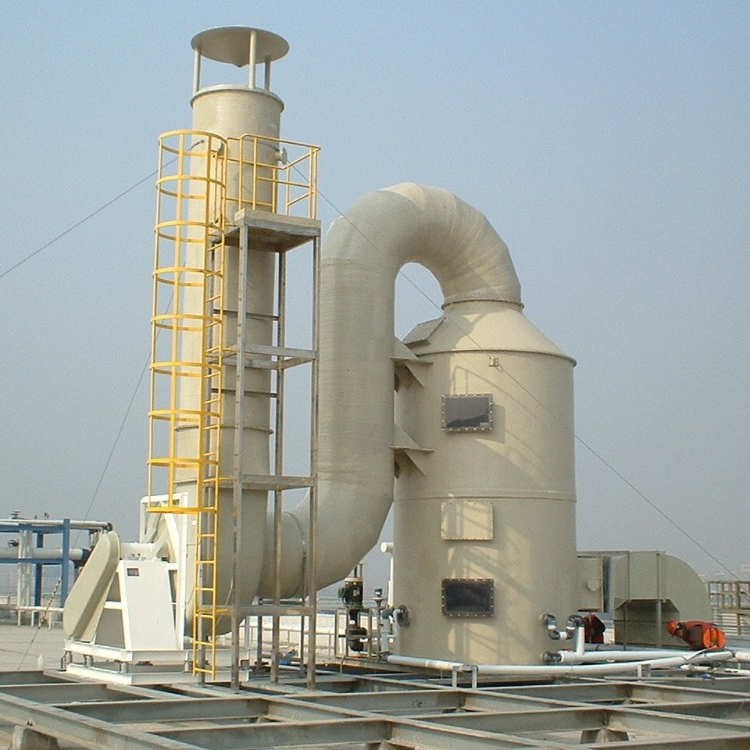
- Advantages: Highest filtration efficiency, high purity, suitable for large scale.
- Disadvantages: High investment and maintenance costs, large installation area.
Pictures of acid filter presses
- Advantages: Low cost, large capacity from 0.5 – 70 m3/h. High durability and easy maintenance.
- Disadvantages: Relatively low filtration efficiency.
During copper electrolysis, the resulting precipitates are treated in a multi-stage process, so that they can be recycled and prepared for refining. To obtain precious metals in a modern and environmentally friendly way, the sludge must be dried to a residual moisture content of less than three percent. Water separation takes place with the help of a membrane filter press.
Precious metal precipitates generated from copper electrolysis are sent to a filter press, where they are filtered and dehydrated.
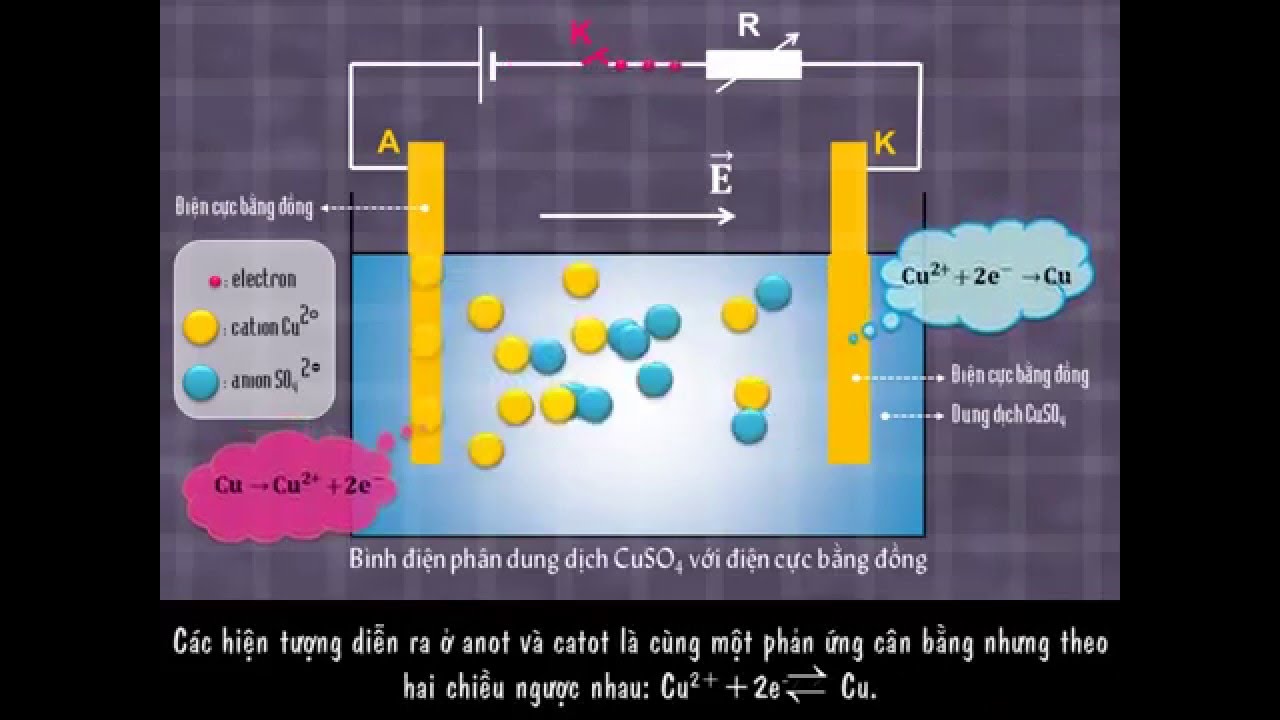
The membrane plate frame press used here is part of an overall process for anode sludge treatment to improve energy savings, recycle resources and reduce emissions. The diaphragm laminator is characterized by its sturdy, durable construction. The applied ABSC (Air Blowing Surface) technology saves energy up to 35% due to the elimination of further processing and multi-stage heating of the anode slurry.
In metal appliances used every day, normally aluminum is always coated with a thin layer of aluminum oxide for the purpose of providing protection against chemical corrosion. The most widely used in the construction industry, the automotive industry, as well as cladding panels. When creating aluminum oxide, a large amount of washing water is generated, this is on the one hand due to the viscosity of the alkaline salt cleaning solution removed in the washing tank, which adheres to the surface of the product.
On the other hand, the process of diffusion of oxides on the surface of the product requires a thorough rinsing after completion of the process. Wash water is collected to the wastewater treatment plant for treatment. At this stage, acidic and alkaline washings are combined and neutralized.
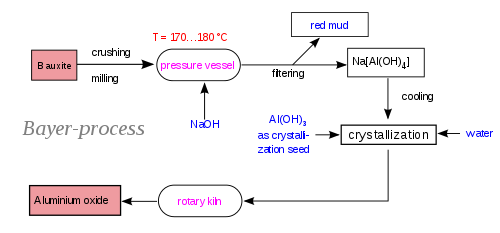
With the addition of flocculating agent, this neutral solution is sent to the filter press. The purified water, without solids, is treated and then discharged into the public sewer system. The filter cake solids (aluminum hydroxide) remaining after pressure filtration in the slurry press are collected in a container and sent to a landfill. With typical design features, the filter press is applied in washing water treatment because of its high filtration rate and durability as well as optimized integrated technology.
The preparation of high purity barium-sulphate* (also called Blanc fixe), used as a filler, is first accomplished by reducing the crude baryte (barite) with carbon and forming a barium-sulphide solution, which is then precipitated by adding sodium sulphate to barium sulphate. The sodium sulfide solution formed as a by-product during precipitation can be returned and recycled.
During the treatment, the precipitated barium-sulphate is filtered by a filter press, dehydrated, and then mechanically dried. The precipitation treatment uses a plate-frame press, which is characterized by sturdy construction, high filtration quality and excellent dewatering capacity. The final step of barium-sulphate production is grinding and packaging.
The filter press shows excellent solid-liquid separation results for biological sludge: a high degree of biological sludge separation (DM content in the filtrate is less than 0.1%), a reduction of nitrogen in the filtrate up to 40 %, reducing phosphorus in the filtrate, the dry content of the sludge cake is up to about 30%.
Ceramic pigments is a temperature resistant material used to produce colored coatings of silicates and to impart flame retardant color to ceramic materials. In wet or dry grinding, the raw materials are crushed, mixed, and then annealed in a tunnel kiln, respectively. After the calcination process, the annealed product is sintered into a block. Colorants (up to about 10 ym) must be filtered off with soluble additives and inorganic salts.
Plate presses are used to filter the suspensions of the crushed material until the required specifications for purity and pigment quality are achieved. The resulting solid is dewatered to a minimum residual moisture, and then heat-dried. Finally, the ingredients are milled and packaged.
The WESTERN FILTER filter press, with its corresponding design features, typical for this application, enables high filtration rates during dehydration, filtration quality as well as dry matter content (DM content) very high, residual humidity low.
Raw materials for the production of ceramic pigments are iron oxide, tin oxide, quartz, calcite, chromium oxide, aluminum oxide, cobalt oxide, alkali chromate, alkaline borate, in addition to vanadium, zirconium and rare earth oxides. Plate frame presses are also used to process and dehydrate the raw materials mentioned above.
In the iron oxide production and processing industry, ferrous sulfate is first dissolved in water, washed, and the raw materials obtained in the form of a suspension are filtered and dehydrated for the purpose of concentration by pressure filtration. From the point of view of energy saving, the most important thing here is the residual moisture content. The membrane filter press all the functions and features required for this process.
The iron oxide pigments are processed by the membrane filter press due to the high filtration-dehydration requirements, which are of vital importance in ensuring energy efficiency throughout the production process. Our products are characterized by typical design features and exclusive membrane filter technology proven in iron oxide treatment, especially where dry matter content can be maximized.
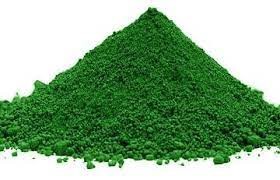
The filter press is used as a separator for mechanical filtration of pigments, which is of great importance in terms of achievable pigment quality, increasing the efficiency of energy saving throughout the production process. With distinctive design features – proprietary membrane filter technology proven in chromium oxide treatment, the WESTERN FILTER plate press offers high filtration rates, high dry matter content, which are critical to manufacture. In this context, it is possible to reduce the drying time at the end of the cycle thereby consuming more than 20% more energy.
Đang cập nhật…
In the iron oxide production and processing industry, ferrous sulfate is first dissolved in water, washed, and the raw materials obtained in the form of a suspension are filtered and dehydrated for the purpose of concentration by pressure filtration. From the point of view of energy saving, the most important thing here is the residual moisture content. The membrane filter press all the functions and features required for this process.
The iron oxide pigments are processed by the membrane filter press due to the high filtration-dehydration requirements, which are of vital importance in ensuring energy efficiency throughout the production process. Our products are characterized by typical design features and exclusive membrane filter technology proven in iron oxide treatment, especially where dry matter content can be maximized.
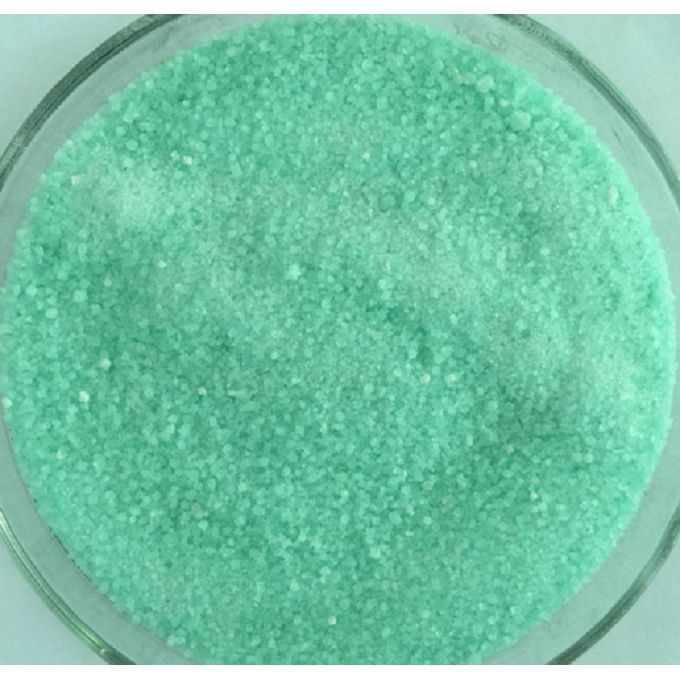
When cleaning the paint containers the production line produces different suspensions. Liquids are pumped out by vacuum pumps to containers for further processing. In the past, liquid sludge was discharged in suitable cascaded collection tanks. The liquid is pumped out and treated in the plant’s own neutralization system. Solids are removed at specific intervals. However, this solid still contains about 70% water.
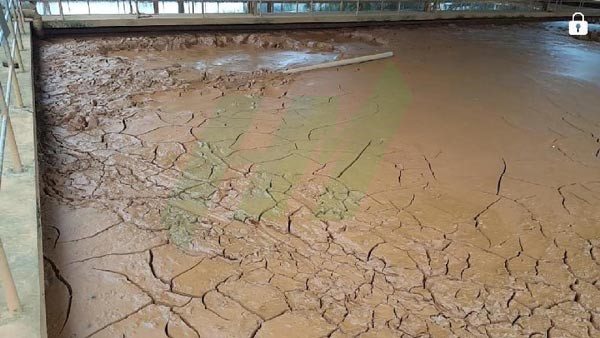
The treatment area basically consists of a receiving station, a solids discharge tank, a sludge tank, buffer tanks, and a filter press. The vacuum pump transfers the suspension to the collection chute. Solids separators transfer solids or foreign objects into a container. After solids separation, the suspension is pumped into the buffer tank. The buffer tanks act as intermediate storage tanks to keep the filtration process by the plate frame press.
The mixed sludge system is supplemented with a small amount of additives. The mud cake has a residual water content of <30%, greatly reducing costs and minimizing human effort.
Filter press are used in the petrochemical industry in many chemical plant and refinery applications. Filtration is a fundamental step in the clarification of many chemicals from iron hydroxide to ethylene glycol. The use of the filter press ensures safe operation throughout its service life.
The membrane filter press has a special feature that the product is mechanically extruded and additionally dewatered in the pressing operation after filtering and washing the filter cake. The result is a higher dry matter content (DM content) resulting in better solubility of the filter cake. Proven plate presses produce high quality end products.
Updating…
Updating…
For the silicic acid production technique, alkaline silicate (soda) solutions are precipitated by adding mineral acids to form amorphous silicic acid and reacted in large stirring tanks at high temperature. To achieve the required final product quality, the suspension is filtered to form a cake (silicate cake). Substances remaining after filtration are released from the dissolved salts (sodium sulphate) during the subsequent washing of the cake, resulting in this process. The residual sulphate content in the filter cake can be adjusted. Membrane filter press are used in this step.
For the production of amorphous metal silicates, alkaline silicate (soda silicate) solutions are precipitated to silicates by the addition of corresponding amounts of calcium, magnesium or aluminum salt solutions and reacted in a stirring bath large at high temperature. Subsequent processing is performed similarly with precipitated silicic acid.
Red sludge or bauxite residue is a waste product, an inevitable side-product in the extraction of aluminum oxide from aluminum-containing ores (especially bauxite), its alkalinity (pH value from 11 to 14), causing serious environmental impacts as well as a major threat to groundwater.
The mixture formed during the Bayer process aluminum production is mainly composed of iron oxide or hydroxide, titanium oxide, aluminum oxide residue, quartz sand, calcium oxide, sodium oxide, and residual sodium hydroxide solution.
At the end of the reaction time, the liquid (alkaline and dissolved calcium/sodium aluminate) is then transferred to a filter press* where it is separated from the solid product mixture (calcium aluminate clay slurry (CATO) and dewatering with the aim of obtaining clear filtrate and sludge cake with maximum dryness.
The sludge cake formed as the end product of filtration has an exceptionally large reaction surface and can be reused in a variety of ways.
Due to the different composition, four applications for bauxite sludge recovery are listed as:
- Recovery of major and minor components: Iron, titanium, rare earth elements.
- Used as the main raw material for the production of products, for example, cement.
- Using bauxite waste as raw materials for the production of building materials such as concrete, bricks and tiles; Soil improvement.
- Transform the rest into a useful product, e.g. with the Virotec process (a process protected by Basecon Technology).
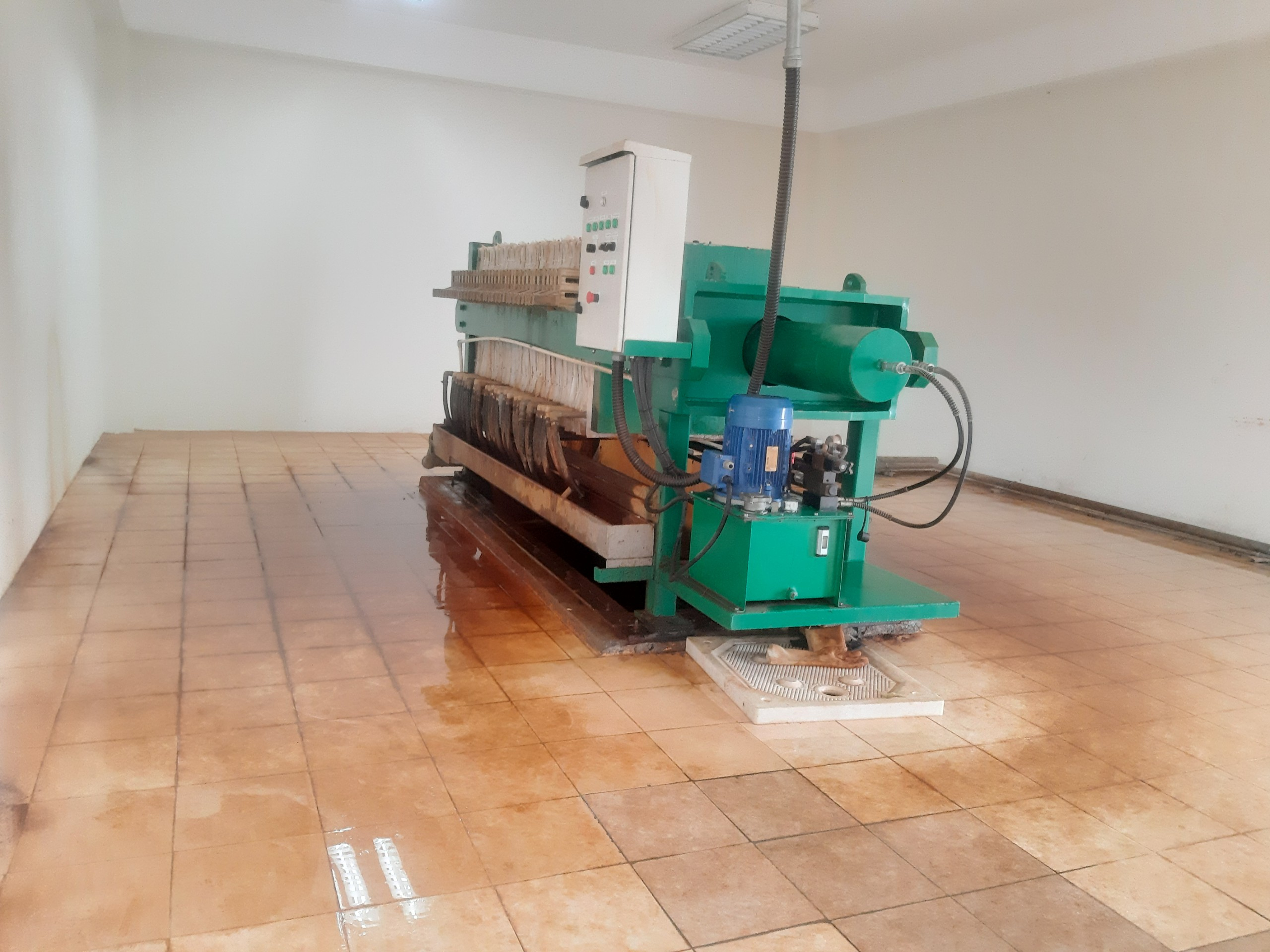
As a result, all process end products are economically and environmentally neutral recyclable materials from red sludge, which were previously considered waste materials.
To produce strontium chromate, the raw materials are dissolved separately in an aqueous solution and combined in a reactor. The starting materials are dissolved in a way that reacts with each other. Due to the high degree of filtration and dehydration required, the suspension is injected into the filter press and mechanically dehydrated with the aim of creating a high solids strontium chromate filter cake.
Filter press are designed with proprietary membrane plate frame technology and proven through high filtration rates. Subsequent washing removes any adherent residues (reaction residues or soluble reagents). The solid fraction obtained and dewatered is dried in the form of lumps in an oven, milled and packed. The dry matter content can be achieved with the membrane filter press which reduces energy consumption by more than 20%.
In the automotive industry as well as in steel mills, tin smelters are required to refine superfine sheet metal into steel grades. The plates undergo many treatments in the steel mill. The purpose is to ensure or increase the corrosion protection of the plate after these processes are completed. The residues generated from the process are sent to the filter press.
In industrial production of titanium oxide (TiO2) titanium ore is finely ground, enriched with concentrated sulfuric acid (up to 30%) which is decomposed into ferric sulphate, titanium oxide sulphate and converted by sulphate (also known as sulphate) process. is the sulfuric acid process).
The decomposition product is dissolved in water. After the initial filtration, the ferric sulfate in solution is washed and separated from the titanium oxide sulfate. This is followed by hydrolysis of the remaining titanium oxide sulfate in solution, which precipitates as a poorly soluble titanium oxide hydrate that is separated. After some filtration, extensive washing, and subsequent bleaching (to remove adherent impurities), hydrated titanium oxide is converted to pure white titanium dioxide in a large tube furnace at 800 to 1000°C.
An essential process for filtering through all stages of the process (chemically aggressive filtration and non-aggressive filtration) is the filter press. Filtration and reduction of washed titanium dioxide by pressure filtration with the aim of producing a filtrate free of solids and titanium dioxide products.
For the vanadium production technique, vanadium ore is converted to sodium vanadate (NaVO3) by adding sodium (sodium chloride, sodium carbonate, sodium sulphate or sodium oxalate) at a temperature of approximately 850 °C in a rotary kiln. After washing with water, filtration, acidification and drying, vanadium vanadate is converted to vanadium(V) oxide*.
In the solid-liquid separation stage, the vanadium salt solution is separated from the by-products by a filter press. The chemical resistance of the material used must be washed regularly due to the mineral acid content in the sludge where the chemical reaction occurs.
To meet these requirements, WESTERN FILTER offers tailor-made solutions with the utmost customer benefit in mind. Our products contribute to high productivity throughout the entire filtration process with their robust, high-quality construction known in the market as well as proven and proven filter cloth, platen and plate technology for this application.
The resulting vanadium oxide (V) serves as a starting material for other vanadium compounds. Another preparation method is reduction with calcium or aluminum to metal vanadium. Most produced vanadium is marketed as ferrovanadium or used as an alloying additive in steelmaking.
To produce zeolites, a siliceous lye is converted with a sodium aluminate solution in precisely defined proportions and under certain reaction conditions.
To achieve the required level of purity and finished product quality of the zeolites, the suspension is separated from the highly alkaline by-products in a complex washing process. They are gently annealed and mechanically removed using a special filter press, with the aim of achieving dry zeolite after crystallization has been completed.
The dry matter content and chemical stability of the materials used are essential due to the high alkalinity of the slurry, which is of great importance. The washing solution and clear filtrate are almost completely returned to the production process. The zeolites are sold as slurry or dried.
In the industrial production of zinc using electrolytic refining, raw zinc oxide is prepared by calcination into a refined ore. Zinc ore is dissolved in dilute sulfuric acid in a chemical process after which impurities of the more precious metal are precipitated by zinc powder. Electrolysis of a zinc sulfate solution is performed using a lead anode and an aluminum cathode, whereby metallic zinc is deposited pure on the cathode.
The products dissolve into solution, but there is no deposition at the cathode. High valence minor elements precipitate as anode slurries. However, the electrolysis of zinc from acidic solutions only works if the zinc salt solution is very pure (only if the potential difference of the hydrogen is so high that the zinc separates instead of the hydrogen).
The filter press is used to clean zinc sulphate. The saturated zinc sulfate solution is filtered, washed, and separated from poorly soluble residues at high filtration temperatures. Cake washing efficiency at filtration temperatures up to 90°C and high resistance to chemically aggressive sludge are of decisive importance and are a fundamental requirement for the system used, filter press components are Selected as filter plate and filter cloth material.
Updating…
Features of Western Filter press for chemical industry
Filter press components used in the chemical industry must be able to meet a wide range of levels of chemical resistance as well as harsh filtration parameters. The know-how is achieved through detailed research and development (R&D) through years of proven experience in the Western Filter product lines. Chemical filtration at temperatures between -10°C and 95°C requires carefully selected materials to ensure stability and resistance.
Washing processes in the chemical industry are often complex, so filter plates design is critical in achieving the required level of wash efficiency. Our standard Western Filter filter plates are ideal for such tasks and have delivered excellent results for many years.
>> Hotline: 0909796560 (Ms. Thanh)
>> Fanpage Facebook: Máy Ép bùn Khung bản – Western Filter Tech
>> Related products: Stainless steel filter press X800 – Western Filter
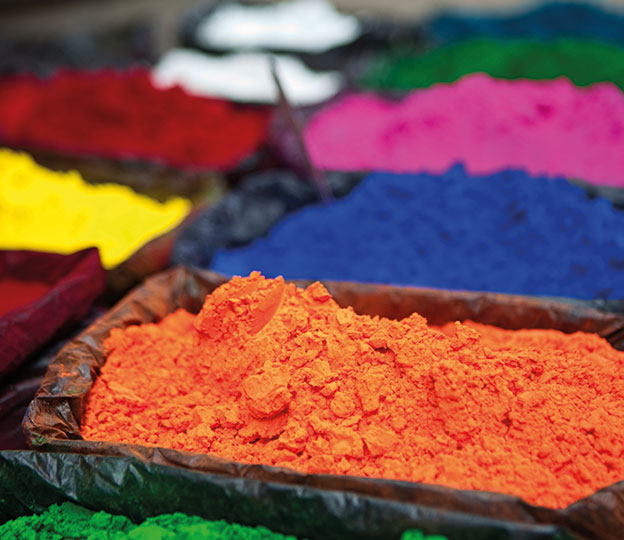
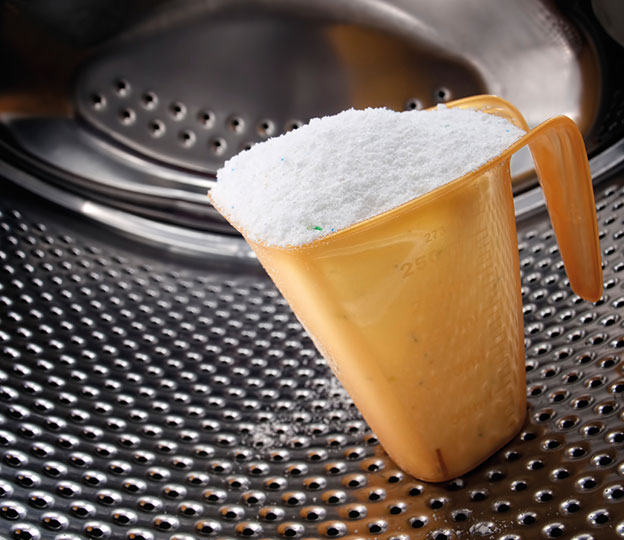
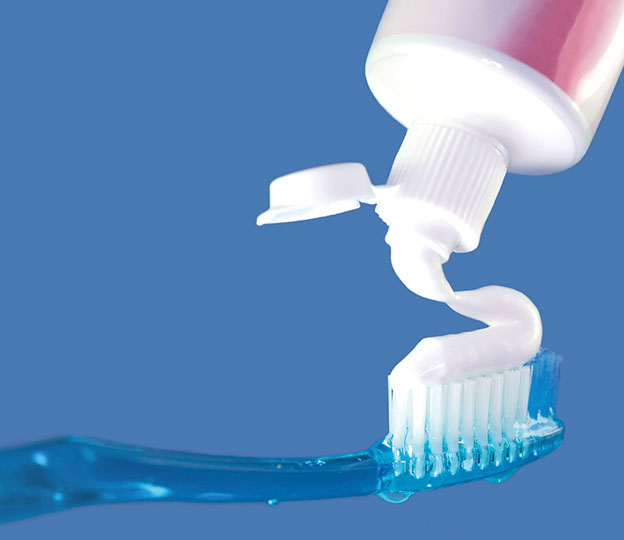
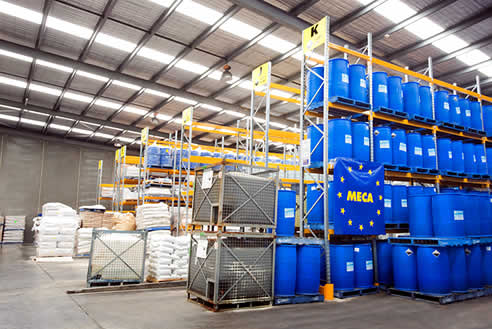
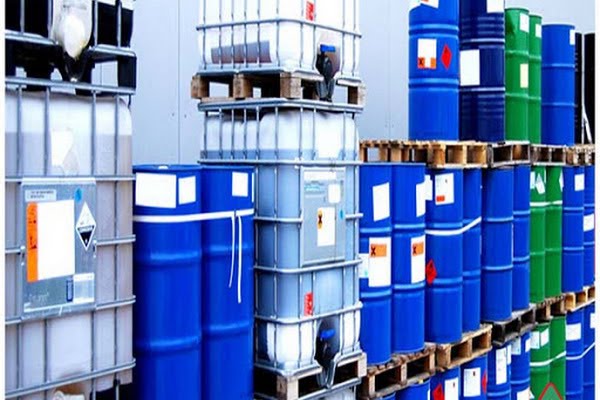
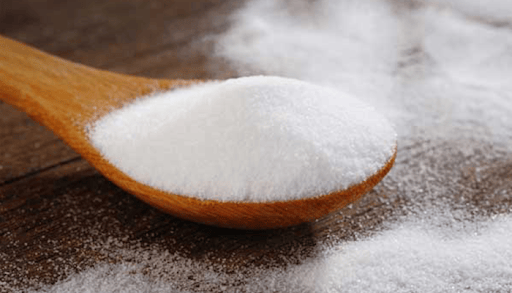