APPLICATION OF FILTER PRESS FOR MINING INDUSTRY
The WESTERN FILTER filter press is used in many mineral processing plants because of its flexibility and optimization in the technological process. The most common applications are dehydration of coal, bauxite, iron ore, nickel, platinum, etc. through solid-liquid separation. The metal ores are pressed in the form of a filter cake of large volume – size. The membrane filter press is preferred because of its high efficiency in quantitative terms in the washing process, the highest dryness due to the pressing pressure at 12-14 bar.
WESTERN FILTER has proven exceptional dehydration technology suitable for a wide variety of mining operations with design features that allow for fast cycle times, high filtration rates throughout the process. Maximum removal of the suspension as well as the water content in the sludge cake. These characteristics are of great importance for capacity requirements and economic efficiency.
SOME TYPICAL APPLICATIONS IN APPLICATIONS FOR MINERAL INDUSTRY
Red sludge or bauxite residue is a waste product, an inevitable side-product in the extraction of aluminum oxide from aluminum-containing ores (especially bauxite), its alkalinity (pH value from 11 to 14), causing serious environmental impacts as well as a major threat to groundwater.
The mixture formed during the Bayer process aluminum production is mainly composed of iron oxide or hydroxide, titanium oxide, aluminum oxide residue, quartz sand, calcium oxide, sodium oxide, and residual sodium hydroxide solution.
At the end of the reaction time, the liquid (alkaline and dissolved calcium/sodium aluminate) is then transferred to a filter press* where it is separated from the solid product mixture (calcium aluminate clay slurry (CATO) and dewatering with the aim of obtaining clear filtrate and sludge cake with maximum dryness.
The sludge cake formed as the end product of filtration has an exceptionally large reaction surface and can be reused in a variety of ways.
Due to the different composition, four applications for bauxite sludge recovery are listed as:
- Recovery of major and minor components: Iron, titanium, rare earth elements.
- Used as the main raw material for the production of products, for example, cement.
- Using bauxite waste as raw materials for the production of building materials such as concrete, bricks and tiles; Soil improvement.
- Transform the rest into a useful product, e.g. with the Virotec process (a process protected by Basecon Technology).
As a result, all process end products are economically and environmentally neutral recyclable materials from red sludge, which were previously considered waste materials.
Sometimes the mineral content fluctuates sharply and the specific properties of bentonite place high requirements on extraction and processing. Bentonites are found in claystones from natural deposits, for example, they are dispersed in water and are of particular practical importance for soil mechanical stability, especially in special foundation engineering and deep drilling.
Because it can have many uses, in this case a significant amount of used bentonite suspensions are produced on different construction sites, which will lose their construction-related properties when containing many soil particles and cannot be used in this form. Furthermore, the treatment of bentonite suspensions by spreading or landfilling in agriculture causes both ecological and economic disadvantages. Therefore, the treatment of bentonite suspension goes through several steps.
The separation of solid particles from the bentonite suspension is carried out in several stages, for example by coarse separation (cleaning by screening), medium separation (following cleaning using hydrocyclone) and finally fine separation.
The second stage of fine separation is achieved by filtration with a filter press, in which the sludge is separated from the mixture. Consistent implementation of the actual separation process based on the WESTERN FILTER filter press will make a positive contribution to the reduction of operating costs and the protection of the environment.
The filtration performed here is characterized by the fact that the ventilated environment – the wet filter media – retains the dehydrated particles, while a compressive force forces the water through the pores of the filter cake and filter clothes. Depending on the requirements, use a membrane filter press or a filter press will be selected accordingly.
Membrane filter press and filter press have the special feature of significantly increasing the dryness that can be achieved in the filter cake through pressing. The reduction in the associated filter cycle time also contributes to higher profitability. The optional blow-dry ABSC technology leads to an additional increase in DM content by blowing out existing pore water in the filter cake. Filter press are available with fully automatic design for fast cycle time and high capacity included.
The production of bleached earth requires the preparation of selected bentonite in multi-stage process steps. First, the raw clay is pre-ground, crushed, and the clay material is plasticized with the addition of water.
The output product from the sludge press is dried using hot air and then ground to the desired particle size. Our filter presses provide optimal solid/liquid separation depending on the DM solids content and batch timing requirements.
The filter press has the special feature of reducing the maximum moisture achievable in the sludge cake through the pressing process. This results in an increased DM content compared to conventional plate presses on the market (membrane technology). The reduction in filter cycle times involved also contributes to higher profitability. The blow-dry ABSC option leads to an additional increase in DM content by purging the water in the existing voids of the sludge cake.
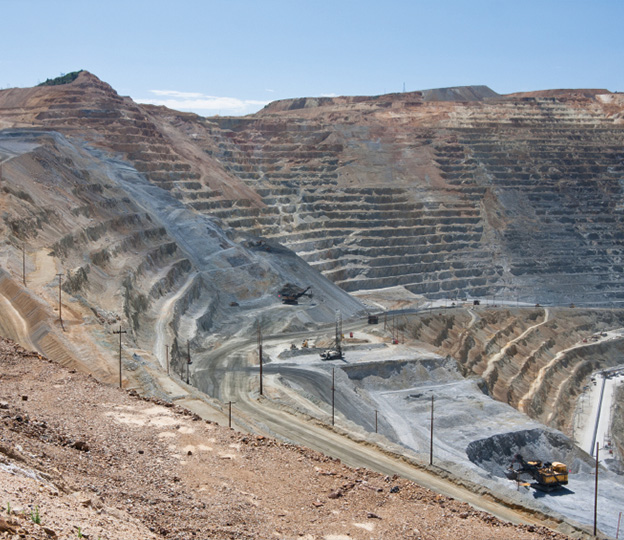

